Rubber
deflashing machine Rubber deflashing machine is versatile machine designed to remove flashes inherent in molded rubber products and zinc die cast products. It has achieved this purpose by taking advantage of the characteristic brittleness of rubber and zinc-alloy in low temperature environment which is generated by the infusion of liquid carbon dioxide or liquid nitrogen ( LN ). The freeze-deflashing method by opted is now an alternative to traditional stamp methods. This freeze deflashing method is able to trim flashes of molds by freezing them first then removing their embrittled portions. For instance, rubber loses its elasticity after being cooled, it first becomes hardened then embrittled and finally cristanlized. Rubber would be so easily reshaped, particularly under the embrittling temperature, by a slight deforming of the material. Molded rubber products ( or zinc-alloy die castings) are filled into the polygonal barrel mixed with and adequate amount of media ( often small metal balls ) and rapidly frozen by exposing to liquid carbon dioxide ( or LN ) then the barrel are rotated. Owing to the difference in hardness of the rubber products and their flashes, the flashes become embrittled much quicker and can be easily removed with the products remain intact. At this stage, the media are thrown by rotation of the barrel thus the deflashing is done in a very short time. Among the conventional freeze-deflashing methods, the use of liquid carbon dioxide ( or LN ) has been regarded much difficult as compared with that of the dry ice. Nevertheless, the automatic operation of rubber deflashing machine has completely overcome all the difficulties of using the liquid gas, as a result, rubber deflashing machine has proved excellent performance in assuring consistent output of high quality products. If you are thinking about enhancing your productivity at the minimum cost, rubber deflashing machine should be your best choice. 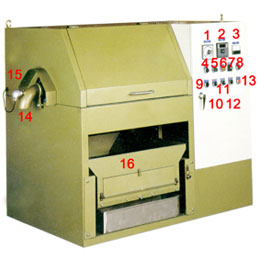
| Structure 1. Timer 2. Thermometer 3. Speed meter 4. Power switch 5. Operation lamp 6. Gas infusion lamp 7. Speed adjustment switch 8. Sieve unit activating switch | 9. Barrel adjustment switch 10. Operation switch 11. Gas infusion switch 12. Timer adjustment switch 13. Gas selection switch 14. Gas vent 15. Thermal sensor 16. Auto selection sieve unit |
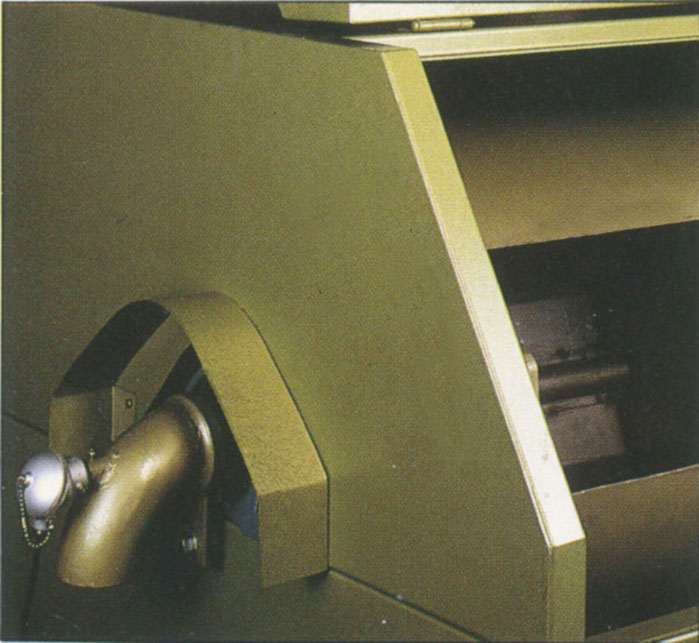
| Inner structure The temperature inside the barrel can be freely controlled in the range of room temperature to -196°C by the automatic temperature control device. The accuracy of this temperature control is the set value with ± 3°C. Coolant Liquid nitrogen ( LN ) As the LN can be cooled down to -196°C, the coolant as optimally-fit to the embrittling temperature of mold concerned. |
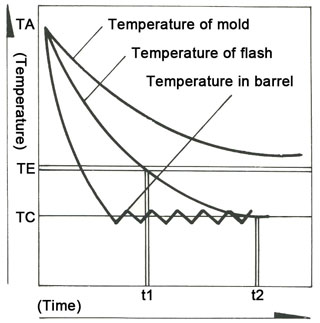
| Temperature fluctuation in operation Owing to the fact that the temperature of flash goes down quicker than the mold itself, deflashing can be done perfectly without damaging the product itself. TA = Room temperature TE = Embrittling temperature TC = Set temperature in the barrel t1 = Barrel operation starting time t2 = Barrel operating stop time |
Examples of the embrittling temperature Products name | Embrittling temperature ( ab ) °C |
Natural Rubber ( NR ) |
- 100°C |
Styrene Butadiene Rubber ( SBR ) |
- 80°C |
Butadiene Rubber ( BR ) |
- 80°C |
Acrylonitrile Butadiene Rubber ( NBR ) |
- 70°C ~ - 90°C |
Butyl Rubber ( IIR ) |
- 110°C |
Neoprene Rubber ( CR ) |
- 110°C |
Silicone Rubber |
-120°C ~ -150°C |
Urethane Rubber |
- 90°C |
Zinc alloy Diecasting |
ab - 40°C |
Samples processed by rubber deflashing machine A = After process B = Before process 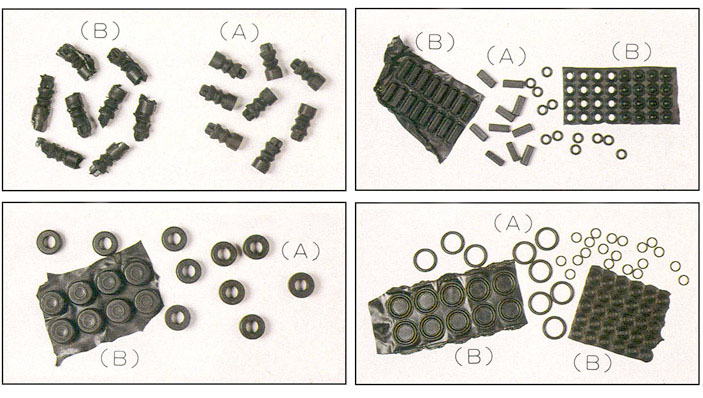
|